LARGE CHAMBER SHEAROGRAPHY SYSTEM
9000
Custom Vacuum Chamber Sherography System
Production Shearography /Thermography System for aircraft composites manufacturing. LTI manufactures the LTI-9000 Vacuum Shearography System that includes the 5100 Shear Camera, Gantry, Part Fixture and Vacuum Test Chamber. Test parts are scanned a section at a time and images may be stitched together in one file.
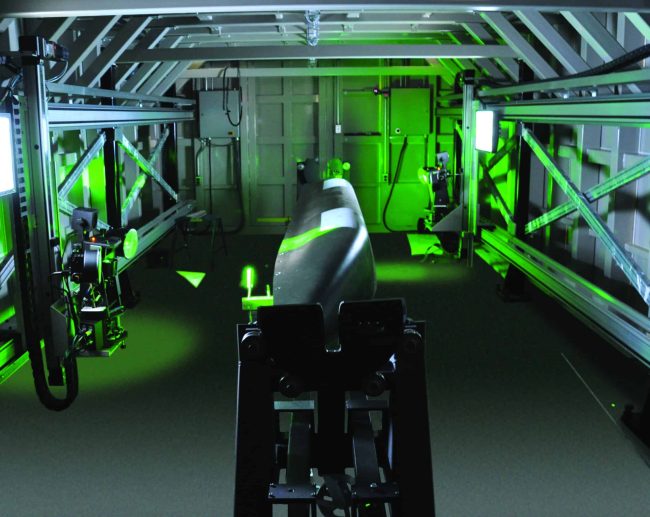
The LTI-9000 Vacuum Test Chamber is manufactured in 8×8, 12×12 ft. cross sections in incremental lengths of 4 feet. Test chambers may be configured to meet your program requirements using modular end door, man-door, and plain sections. Chambers are manufactured complete with blower and control valves, electrical wiring harness, interior lighting and optional closed circuit video.
LTI provides complete installation, certification and training.

Camera Gantry allows vertical and horizontal motion through the full volume of the test chamber and operates in manual or automatic modes with Teach/Learn capability. Test part throughput of 200-500 sq. ft. per hour is typical.
LTI Advantage
Shearography Vacuum Test Chambers have unique design features optimized for mechanical stability, high cycle rate, low noise, industrial safety, and laser safety. They are typically designed in 4 foot segment lengths, width and height. This design may be changed due to the customer size requirements: The chamber is typically provided with one (1) End Door and, one (1) Side Man Door. Test chambers are designed for a maximum operating pressure differential of 0.3Bar (4.41 psi).
Custom Integrations
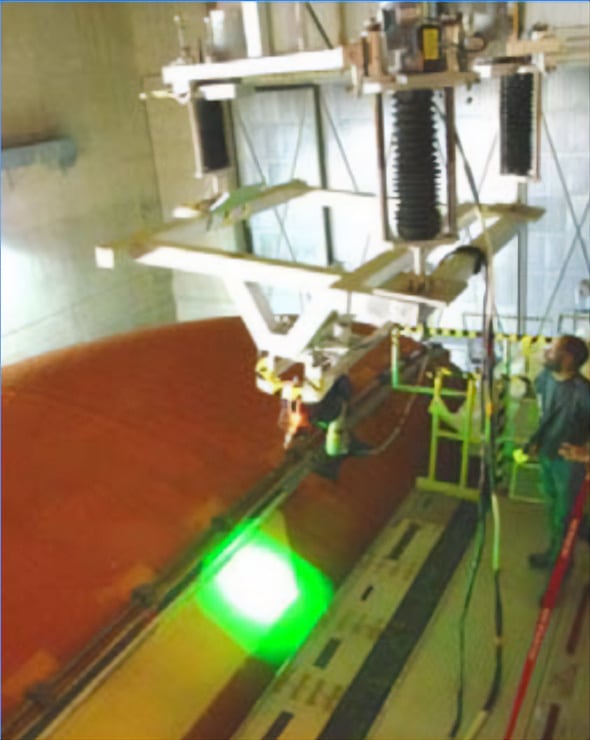

LTI has more experience than any other company in the world building production shearography systems meeting the industry needs for in-line shearography inspection of aircraft and aerospace components. LTI continues to be the leader in the laser shearography industry with the latest in innovations of technology application of software and hardware.
Downloads
Patents: The LTI-9000 is manufactured in the USA under US and foreign patents 6,717,681; 5,257,088; 5,094,528. Additional patents pending. Specifications are subject to change.
Laser Shearography Certifications AIA NAS 410, ASNT SNT-TC-1A, ASTM E2581-07, EN 4179


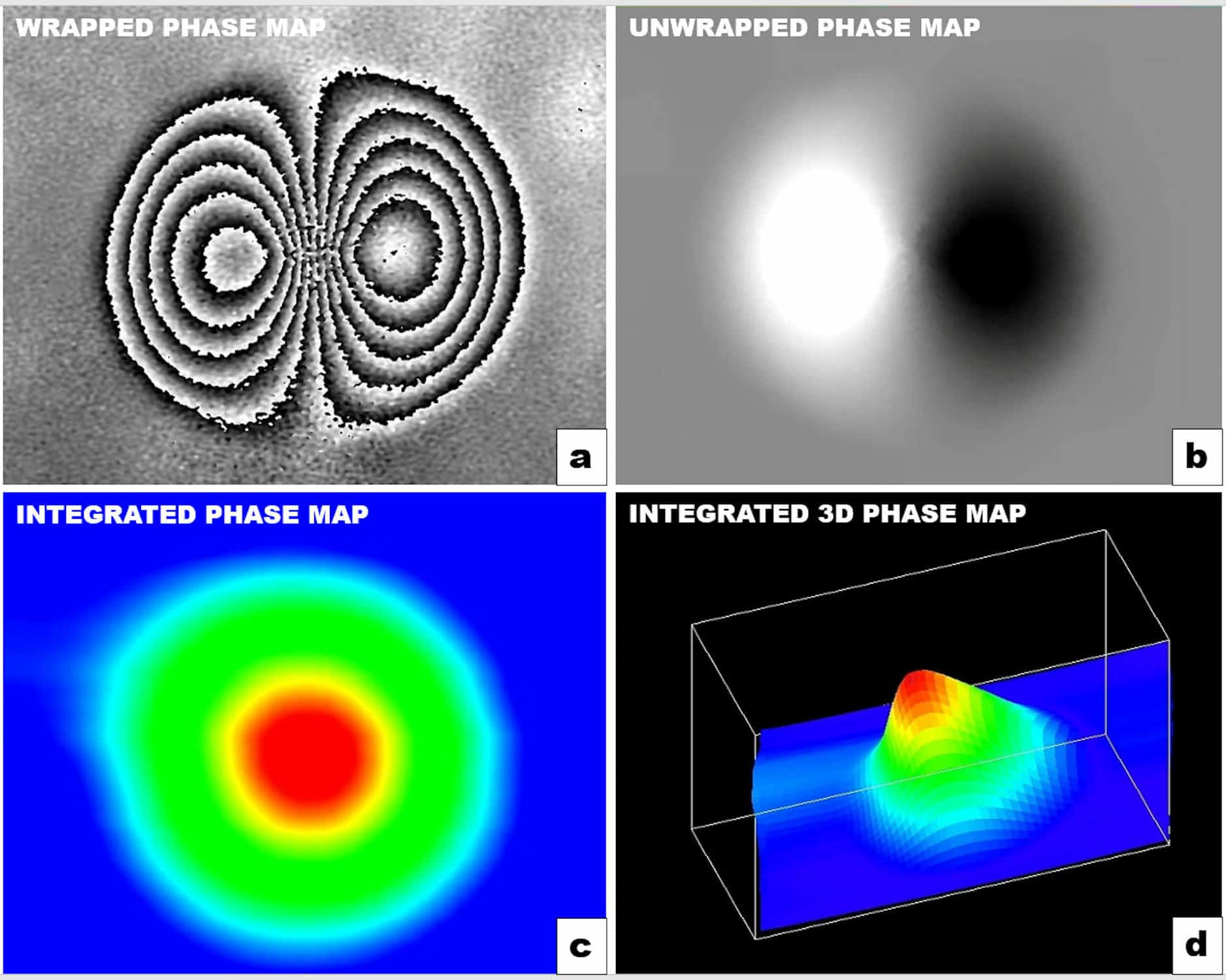
INSPECTION APPLICATIONS
SHEAROGRAPHY IN ACTION



OUR FULL LINE OF SHEAROGRAPHY NDT SYSTEMS
Shearography can be applied to many applications, if we don’t have a system that works for you, we can custom build one that will.